Target zero waste: building “second-hand” to revive materials
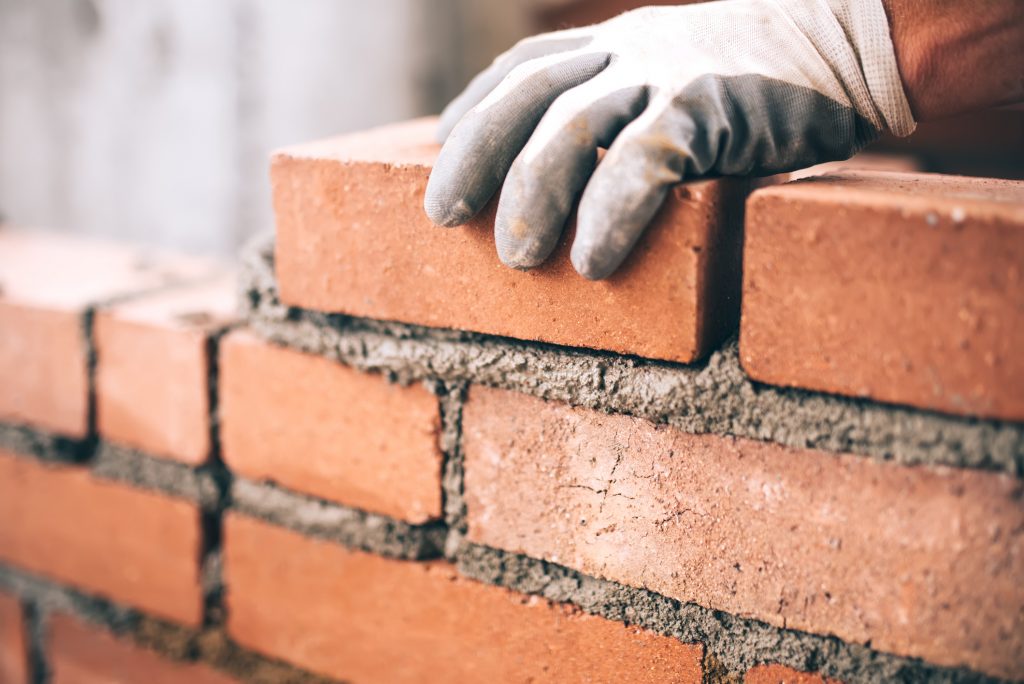
Salvaging and reusing materials to rethink the building stock of the future. From second-hand dealers to circular materials directories, how some cooperatives, architects, and EU projects are revolutionizing the construction works.
Victoria is a chief financial officer in a small biotech company in the Brussels area. After renting a flat together for several years, she and her husband Quentin bumped into the house of their dreams in 2019. Located in a vibrant district, it was a typical 4-storey “Brussels house” with high ceilings, a small garden, and just the hint of charm which made it unique. “Since the previous owner was a carpenter, he had customized it with very personal touches. It had a ‘soul’, and every detail spoke of its history,” she recalls. “Hence our idea of preserving its spirit as much as we could.” However, Victoria and Quentin’s house had a problem. Many problems, indeed. Being quite old, the heating, insulation and electrical system needed a lot of renovation. But instead of turning to global franchises and new materials, the couple mainly relied on what they found on the spot or via second-hand dealers: “We used the doors of the old kitchen for our bedroom, placed the wooden cladding of the facade on some of the ceilings and even moved two windows and a staircase from the garden side to the interior.”
Victoria and Quentin did what is known as ‘salvaging’: the recovery and reuse of materials that would otherwise go straight into the trash. Indeed, over 35% of all the waste generated in the EU comes from the construction sector. Both already sensitive to ecological motives, they were counselled by a small local firm of architects that specialised in reclaim and reuse. “I present myself as an ‘eco-anxious architect’”, says Nicolas Périer, one of the partners of VLA Architecture. “We care about limiting emissions. We tell it straight away to our clients, and then, if they like our approach, we might happen to push it well beyond what we had originally envisaged”. This is exactly what happened to Victoria and her husband: “After reusing all that we could, we still needed a lot of furniture and materials. We started looking around and we ended up buying 75% of them from second-hand dealers: an old bathtub, some red bricks for our terrace, and all the radiators, which alone allowed us to save around €10 000,” she says.
What made it possible to push the salvaging so far was also the work of RotorDC, a Belgian cooperative aimed at fostering reuse practices and supporting private and public building owners in their renovation works. Being “as generous with Brussels as the city is with us” is the claim resuming their philosophy. “People bring us their materials, we store them in our facilities and once we sell them, we share the profits,” says Michael Ghyoot, project manager at Rotor, the non-profit firm at the origin of the cooperative. But such a win-win strategy was just a first step. To foster good practices in the construction sector and reach out to all of its different stakeholders, Ghyoot and his colleagues also launched Opalis, a directory listing the reclamation and salvage dealers of the region: “We were frequently asked: ‘What can I do with this batch of bricks retrieved from my site?’ or ‘Where can I find some second-hand tiles?’ We realized then that there was a real need both from owners and the mainstream construction industry, and we decided to connect them and shed more visibility on such dealers, which are real frontrunners of the circular economy.”
Crucial for the uptake of such a market is providing customers with guarantees on the materials’ origin and quality. This is why Salvo, a UK-based marketplace displaying salvage dealers also in France, US, and Australia, created a “code” and a “label”. While the first one is an “assurance for good practice in sourcing for businesses”, the label is “designed to certify that the materials are truly reclaimed,” says its CEO, Sara Morel. In Spain, the researchers of the Catalonia Institute of Construction Technology (ITeC) are pushing this approach even further: “We are working at a European marketplace reserved for certified circular materials, and based on their geolocalization. The idea is not only to provide a virtual meeting point for supply and demand but also to be guarantors of their circularity,” explains Tommaso Giomi, architect and researcher in the sustainable construction department. Not all of them will be immediately available, but from cements and resins to bricks and industrial conglomerates, some 30 000 items are already registered in ITeC’s database with information such as the machinery, the workforce, and the water consumption needed for their installation.
Developed within an EU-funded project promoting circular practices in the housing sector, this marketplace is part of the project’s legacy: “Houseful will come to an end in the next few weeks, but it will be survived by a digital platform, aimed at both connecting all the sector’s stakeholders and evaluating buildings’ circularity. Technically known as “Saas”, an acronym for “Software as a service”, it has been developed by the Spanish engineering company IRIS. “On the one hand, we created a kind of a LinkedIn of the building sector: an interactive directory to facilitate connections between those seeking and offering services and materials,” says its project manager officer, Albert Torres. “On the other hand, we simplified the procedures by gathering on the same platform services which are usually provided by very dispersed players.” Targeting construction companies, municipalities, and policymakers, this “circularity tool” allows a self-evaluation of the new and the existing building stock, by simply filling out an online form: “Once you provide information such as the construction materials, the overall surface and the number of windows, the system calculates their circularity in terms of CO2 emissions, energy use, and so on.” The end goal is to facilitate a ‘circularity-driven’ decision-making process: “For tenders, it will for instance allow urban planners and local councils to compare different projects according to common parameters. But it will also help municipalities to evaluate how much of their building stock needs to be refurbished,” explains Torres.
A shared ambition of this wide range of initiatives is to promote reuse practices, which are still very limited in the construction sector. “If on a building site, we manage to recover 10% of the materials it is already an extraordinary result. Most of the materials are simply not made to be dismantled without being torn to pieces,” says Périer. To put it with Ghyoot, this is because “waste is a matter of political will. It says a lot about a society.” And with the latest figures revealing that in North-Western Europe only 1% of building elements are reused, it seems to reveal a society “deeply in need of a change of mindset”. “For the circular approach to be effective we must first realize that we have to start conceiving our building stock differently,” says Giomi. “Only once it has been designed from the beginning as a proper bank of materials to be reused for further purposes, will a significant cut of construction waste be within reach.”
(Article written by Diego Giuliani)
Photo credits: Unsplash